DIFFERENT CONVENTIONAL EMI SHIELDING PROCESS TYPES
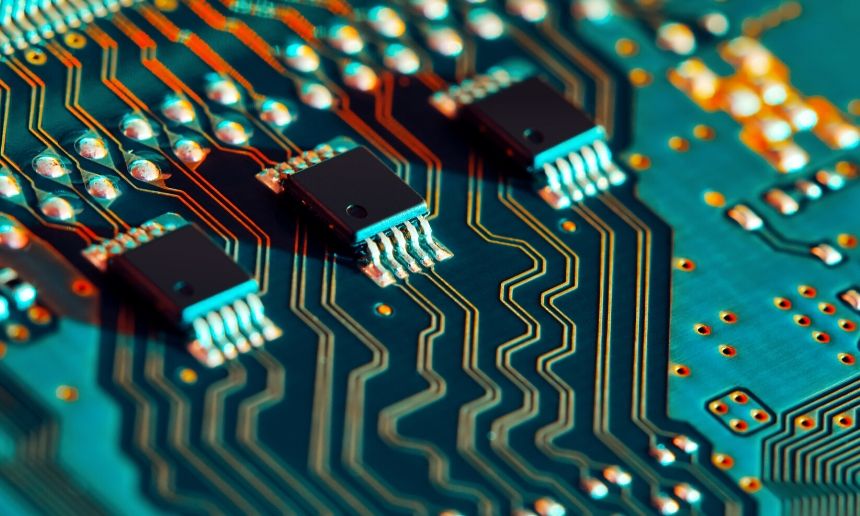
There are several aspects involved in preventing devices’ electromagnetic wave interference (EMI). When looking into different EMI shielding process types for conventional EMI Shielding, enclosure configuration and the material used are two important considerations.
Enclosure Configuration
Blocking EMI first depends on if and how you enclose your device. To prevent EMI, you must choose an optimal configuration for your specific device. Of the EMI shielding process types, one simple and effective option is Volumetric Shielding (or Faraday Cage). This is a six-sided box that entirely encompasses your device and effectively prevents EMI but doesn’t allow very much airflow. Perfect for military-grade devices that need to be impenetrable, Faraday Cages are difficult to implement in modern devices with branching inputs and outputs that also need shielding. You can shield more locally by covering the circuit board, and you can even choose stick-on sheets to isolate very specific or hard to reach areas of your device.
Metals
The material your enclosure consists of is a secondary consideration because the materials’ properties determine your costs, flexibility during construction, and the ability to limit interference. Copper, aluminum, steel, and nickel are relatively heavy and costly materials that are conductive and effective at blocking EMI. Copper is an expensive yet particularly malleable option that fits many uses.
Plastics
Recent innovations in EMI shielding process types have allowed professionals to use plastics instead of metals because they’re cheaper, quicker to manufacture, easily shaped, and lighter than metals. To ensure they are as capable of limiting device EMI, they need to have a conductive layer applied. Two important processes for conventional EMI shielding are vacuum metalization and electroless plating. When vacuum metalizing plastic, a metal vaporizes and deposits onto a pre-treated plastic, onto which it condenses and forms a thin metallic layer. In electroless plating, on the other hand, experts typically immerse the plastic in a nickel or copper ion solution to form a conductive metallic bond.